This article will delve into the basics of pitch diameter, shedding light on its definition, significance, applications across industries, and the crucial role accurate measurement plays in maintaining quality standards.
A Brief History of Pitch Diameter
In 1841, "Joseph Whitworth developed a screw thread design that was adopted by major English railroad companies and quickly spread across the country. His papers on screw threads exposed the “evils” of figuring out thread pitches without a uniform standard. While Whitworth admits that any standard would be based on largely arbitrary decisions, and there would always be special cases that don’t fit the standard, he cautions that there is more to be lost by delaying and urges the attention of engineers across the nation. With the support of the railroads, then the Royal Dockyards and shipping companies, Whitworth’s 55-degree thread, with rounded edges and simple table of pitches spread nationally."
Source: https://evolventdesign.com/blogs/history/whitworth-and-the-history-of-pitch
However, the concept of screw design can be traced to Archimedes. "Archimedes screw is named after Greek mathematician Archimedes who first described it around 234 BC, although the device had been used in Ancient Egypt long before his time.[3] A screw conveyor is a similar device which transports bulk materials such as powders and grains."
Source: https://en.wikipedia.org/wiki/Archimedes%27_screw
Without standardization, there would be no assurance that a bolt from one manufacturer would fit a nut from another. Problems arise when different countries used different standards for threads. In the United States ANSI - American National Standards Institute - played a pivotal role in developing thread standards. ANSI has developed standards for:
General Purpose Screw Threads
General Terminology and Methods
Aerospace Screw Threads
Understanding Pitch Diameter
Definition and Significance:
Pitch diameter, in simple terms, is the diameter of an imaginary cylinder that passes through the threads of a screw or the crest of a thread on a nut. This concept is fundamental in threaded fasteners and mechanical assemblies. The significance of pitch diameter lies in its role as a determining factor for the proper engagement of threads. It acts as a reference point, ensuring that the male and female threads fit together seamlessly.
Pitch diameter is not an arbitrary dimension; it directly affects the strength, reliability, and functionality of mechanical components. In threaded connections, it serves as a critical parameter for maintaining the integrity of the assembly.
Ensuring Proper Thread Engagement:
Proper thread engagement is vital for the stability and reliability of mechanical structures. The pitch diameter ensures that the threads on a fastener properly mate with those on a corresponding nut or threaded hole. When the pitch diameter is accurately maintained, it prevents issues such as loose connections or over-tightening, both of which can lead to compromised structural integrity.
Pitch diameter acts as a safeguard against potential threading problems, promoting optimal performance in various mechanical applications. Its role in ensuring proper thread engagement is particularly crucial in industries where precision is non-negotiable.
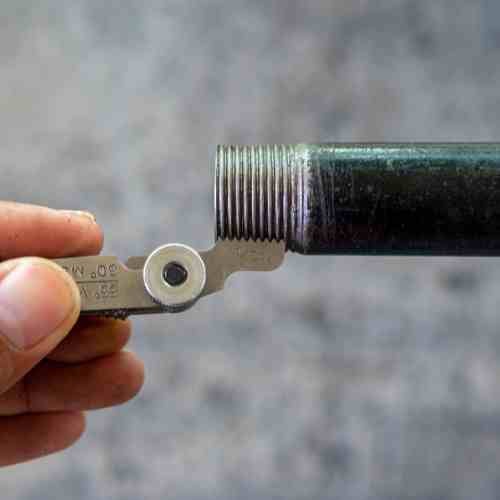
The Role of Pitch Diameter in Fastener Performance
Pitch diameter plays a critical role in determining the performance of a fastener. Deviations from intended pitch diameter specifications can lead to improper thread engagement, compromising the structural integrity of the assembly. In industries where reliability is paramount, such as aerospace and automotive, the consequences of suboptimal pitch diameter can be severe.
For engineers and designers, understanding the role of pitch diameter is essential. It differentiates a fastener that merely fits from one that excels in performance under diverse conditions.
Pitch Diameter Measurement Techniques
Accurate measurement of pitch diameter is a cornerstone of ensuring the quality of fasteners. Various techniques are employed, with each method chosen based on the specific characteristics of the fastener in question.
One common method involves the use of precision instruments such as micrometers or optical comparators. These tools enable engineers to measure pitch diameter with exceptional accuracy, providing crucial data for quality control. In an ISO certified supplier environment like Blue Chip Engineered Products, these measurement techniques are not optional but integral to the quality control process.
Pitch diameter precision finds application in a myriad of industries, each with its own unique demands for reliability and performance. The aerospace industry relies on precise pitch diameter in aircraft assembly to ensure the structural integrity of critical components. In automotive manufacturing, the pitch diameter is a key player in vehicle assembly, contributing to safety and overall efficiency.
Applications in Different Industries
Industry | Application | Significance |
---|---|---|
Aerospace Industry | Aircraft assembly, rocket manufacturing | Precision in pitch diameter ensures the integrity of fasteners in critical aircraft components. |
Automotive Industry | Vehicle manufacturing | Pitch diameter precision contributes to vehicle safety, performance, and fuel efficiency. |
Energy Sector | Oil and gas exploration, power generation | Accurate pitch diameter in fasteners is crucial for stability in energy infrastructure. |
Construction and Infrastructure | Building construction, bridges, tunnels | Precision in pitch diameter is critical for the stability and durability of constructed infrastructure. |
Medical Devices Manufacturing | Production of medical equipment | Threaded fasteners with precise pitch diameters ensure reliability in medical device assembly. |
Telecommunications | Manufacturing of communication equipment | Pitch diameter accuracy is vital for stability and reliability in telecommunications infrastructure. |
Defense and Military Applications | Defense equipment manufacturing | Threaded fasteners with precise pitch diameters are essential for robust military components. |
Electronics Industry | Production of electronic devices | Pitch diameter precision is crucial for reliability in the assembly of electronic components. |
Railway and Transportation | Manufacturing of trains, locomotives | Accurate pitch diameter contributes to safety and efficiency in railway transportation. |
Marine and Shipbuilding | Construction of ships, submarines | Precision in pitch diameter ensures structural integrity in marine and shipbuilding applications. |
The significance of pitch diameter extends across various industries, each with its own unique demands.
Measuring Pitch Diameter
Overview of Common Techniques:
Accurate measurement of pitch diameter is essential for maintaining quality standards in manufacturing. Various techniques are employed to measure this critical dimension. Common methods include using precision instruments such as micrometers, calipers, and optical comparators. These tools allow engineers and technicians to gauge the pitch diameter with a high degree of accuracy.
Micrometers, for instance, directly measure the pitch diameter by capturing the distance between opposite threads. Optical comparators use visual magnification to inspect thread profiles and determine the pitch diameter indirectly.
Importance of Accurate Measurement:
The importance of accurate pitch diameter measurement cannot be overstated. It is a quality control measure, ensuring that threaded fasteners meet design specifications. In industries where precision is paramount, such as aerospace and automotive manufacturing, deviations from specified pitch diameter values can lead to catastrophic failures.
Accurate measurement also aids in identifying potential manufacturing issues, allowing for corrective actions before the final product is assembled. This proactive approach is crucial in maintaining the reliability and safety of mechanical systems.
Benefits of Choosing an ISO-Certified Fastener Supplier
The advantages of sourcing fasteners from an ISO-certified supplier go beyond a mere checkbox on a procurement list. For engineers and designers, it translates to confidence that the fasteners they integrate into their designs have undergone rigorous quality checks, including meticulous scrutiny of pitch diameter.
ISO Certification and Quality Assurance
Blue Chip Engineered Products is an ISO-certified fastener supplier. ISO standards provide a robust framework that governs every aspect of the manufacturing process, ensuring that each fastener adheres to stringent criteria for precision and reliability. Regarding pitch diameter, ISO certification becomes crucial in maintaining consistency across the product lines supplied by Blue Chip Engineered Products.
This stringent quality assurance process, intrinsic to an ISO-certified supplier like Blue Chip Engineered Products, directly influences the precision of pitch diameter. The certification serves as more than just a badge; it guarantees that every fastener leaving the facility meets the highest standards of accuracy.